Disperse Print Fabric is a printing process that uses disperse dyes to color polyester fabrics. This method is suitable for small-run, high quality printing, and can be used in combination with other types of prints. It is less labor intensive than screen printing, and it produces a more durable result. It also allows the use of a greater variety of colors, and it can be used on more complicated designs than the screen printing method can.
Unlike pigment printing, which uses large quantities of dyes to color the fabric, disperse dyes are printed with smaller amounts of colorants. The process also involves a higher temperature, which allows the colorants to penetrate into the fibers. However, this process is still slow, and it can produce a limited number of colors per batch. Disperse dye printing can be used on a wide range of fabrics, including cotton, silk, and nylon. It is also suitable for apparel, as it has a high resistance to crocking and perspiration.
The printing of textile material is done in either direct or transfer style. In direct printing, the dyes are applied directly to the fabric. This is the most popular printing method today. The transfer method, on the other hand, requires a lot of preparation, which can lead to an increase in production costs. In addition, the fabric may not have the same characteristics as the original one. Moreover, the printed surface is likely to be rough. Nevertheless, both methods have their own advantages and disadvantages.
In disperse printing, the dyes are dissolved in water to form a dispersion. In addition, a wetting agent is added to the mixture in order to make the dyes wet the fabric. Then, a thickener is added to the mix to help keep the dyes in dispersion. The thickeners that are used for this purpose include starch ethers, modified locust bean gums, and carboxymethyl cellulose. The disperse dyes must be fast to steaming and thermofixation. Therefore, they should not be affected by alkali and acid liberation during the fixing process.
After printing, the resulting fabric is steamed to fix the disperse dyes. This step is crucial to the durability of the printed fabric. It is also important to remove the excess thickener and dyestuff from the surface of the fabric. This prevents the fabric from becoming brittle and scratchy. The steamed fabric is then washed and dried to obtain the desired final product.
The use of disperse dyes for washing-free printing is a promising alternative to traditional printing technologies. Disperse dyes have good permeability and fastness properties, which allow them to penetrate the polyester fibre. This type of printing has great potential in the textile industry, as it can be produced in small batches and in a short time. In addition, this technology reduces the pre-printing treatment and washing processes, which helps to improve environmental sustainability in textile production. This is an important step in the development of polyester as a new material for sustainable fashion.
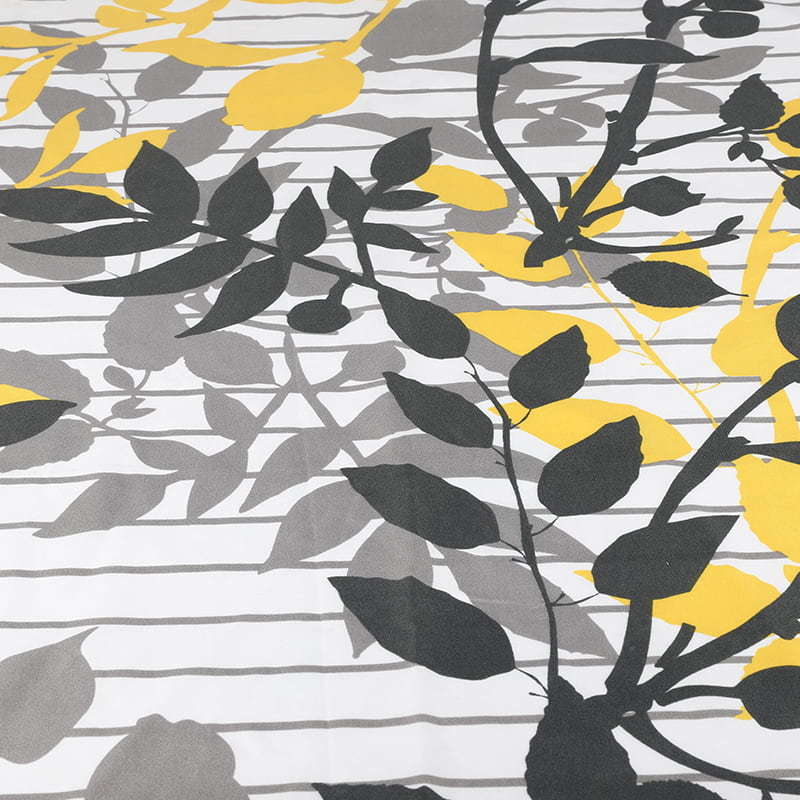
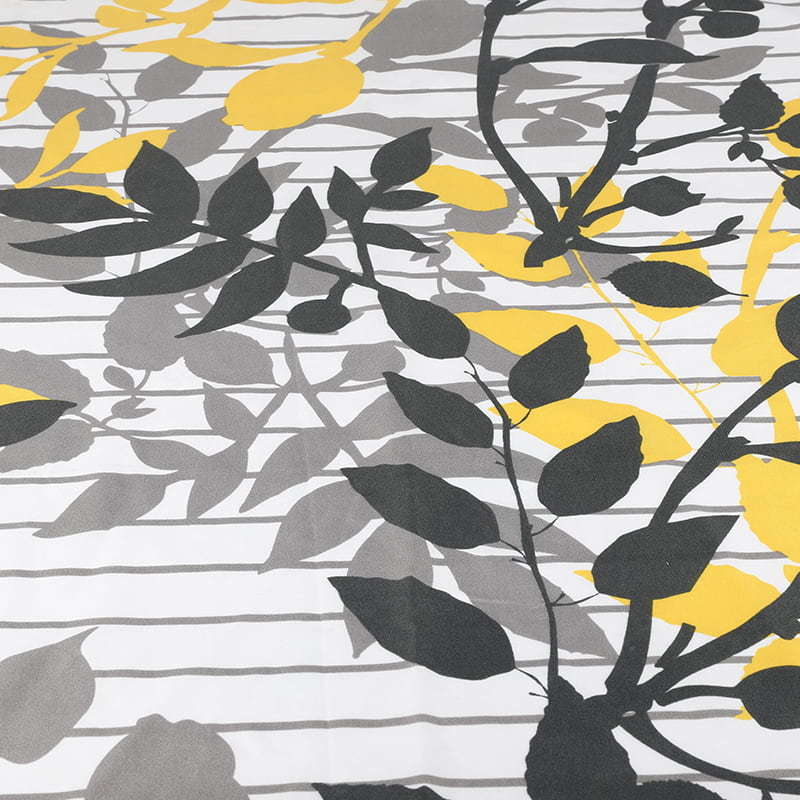